The name “sandpaper” originates from the time when this sanding tool had just been invented and back then the main abrasive material was minerals extracted from the nature, which were thinned and sieved, and the resulting sand was attached to the paper with glue. Nowadays, minerals of natural origin are used in the production of abrasives increasingly less and abrasives are mainly made synthetically. So, the name “sandpaper” is misleading and should be replaced with the name “sanding paper” and in a broader sense with the names “sanding materials” or “abrasives”. Thanks to its great strength, persistent sharpness and durability, natural minerals are almost exclusively superseded by synthetic minerals. Different synthetic minerals are used as abrasives, but when sanding wood, the two main abrasives used are aluminium oxide and silicon carbide.
Aluminium oxide (AL₂O₃) is hard, tough and can resist high sanding pressure. Less sharp edges and irregular shape are also characteristic to aluminium oxide (also corundum). It can be used for both soft and hard wood. As the sanding result is rougher compared to silicon carbide, aluminium oxide is more suitable for calibration and for high stock removal.
Silicon carbide (SIC) is the hardest abrasive grain. The silicon carbide has a different shape and other cutting properties than aluminium oxide. It is characteristic to silicon carbide that an individual grain is sharper and several sharp edges can be used simultaneously because the grain is better shaped. At the same time, silicon carbide is more friable/fragile and can’t withstand high sanding pressure. If the pressure is too high, it will result in breakage of the grain and shorten the lifetime. Silicon carbide cuts the material clearly and gives a better (fibre free) result. Suitable for intermediate sanding of soft wood, finishing of hard wood, sanding of MDF and other surfaces.
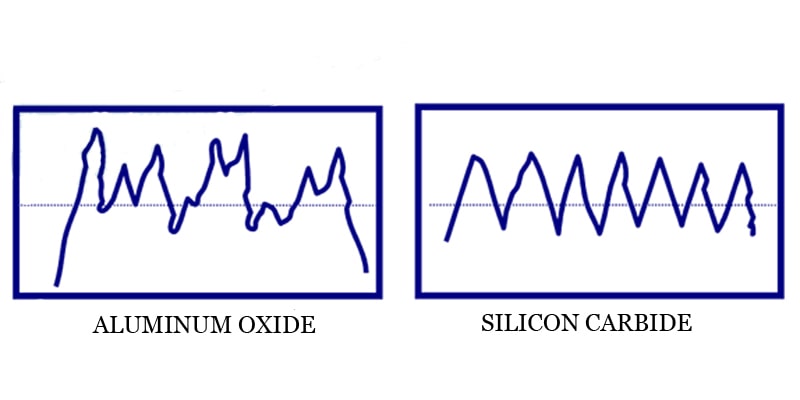
The closeness of the synthetic minerals on the backing can greatly affect the sanding result. The basic rule is that the closer a product is coated, the better finish on the sanded surface because a close coating leaves less space between dust and other particles.
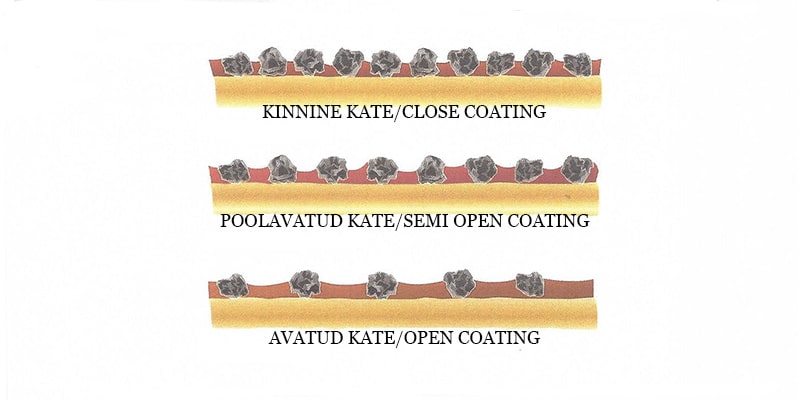